مستربچ
مستربچ، یکی از محصولات پرکاربرد در صنعت تولید است که بهخاطر ویژگیها و مزایای فراوان خود به عنوان یک ابزار کاربردی و اساسی شناخته میشود. این محصول با ساختار گرانولی خود، سهولت در ذخیرهسازی، جابجایی و استفاده را فراهم کرده و بهعنوان یکی از ابزارهای کلیدی در محیطهای صنعتی و تولیدی شناخته میشود.
در این مقاله به بررسی مختصر انواع مستربچ، اجزای تشکیلدهنده آن، و فرآیندهای تولید آن خواهیم پرداخت. همچنین، مزایا، ویژگیهای یک مستربچ کیفی، و درصد استفاده از این محصول در صنایع مختلف را نیز بررسی خواهیم نمود. این مقاله به شما کمک خواهد کرد تا با جزئیات و کاربردهای متنوع مستربچ آشنا شوید.
معرفی مستربچ
مستربچ به عنوان یک محصول، به این صورت توصیف میشود که در آن پیگمنت و یا افزودنیهای دیگر به صورت بهینه در یک رزین پایه و یکپارچه میشوند. این افزودنیها شامل مقدار زیادی پودر رنگ (پیگمنت)، پرکنندههای معدنی یا مواد شیمیایی میباشند که به سه منظور مختلف اضافه میشوند: تولید رنگ، بهبود خواص، و یا کاهش قیمت تمامشده به پلیمر. پایه پلیمری مستربچ عمدتاً باید خواص مشابه پلاستیک اصلی را داشته باشد و شکل ظاهری آن به صورت دانهای (گرانول) ظاهر میشود.
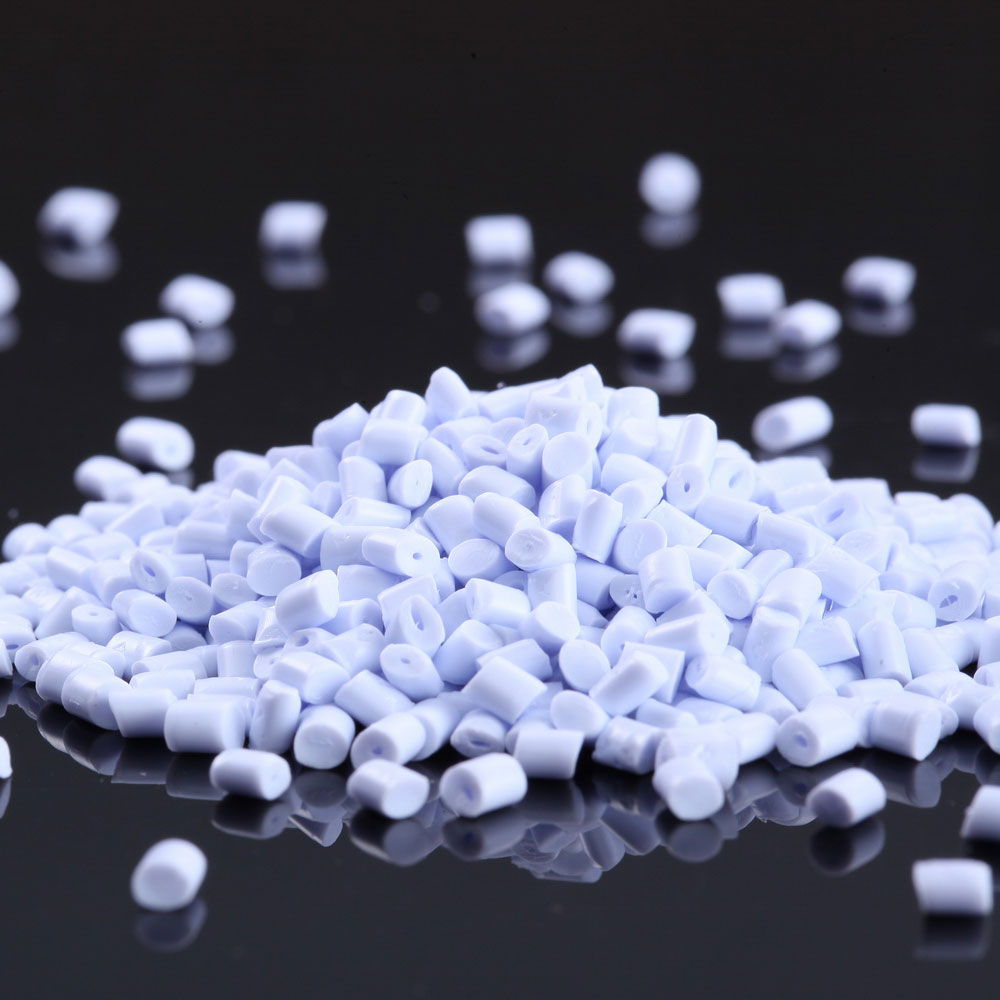
بررسی اجزا مستربچ
مستربچها از سه جزء اصلی تشکیل شدهاند که هرکدام نقش مهمی در ترکیب و خواص نهایی محصول ایفا میکنند.
- 1. پلیمر پایه:
پایه پلیمری معمولاً از انواع پلیاتیلن، پلیپروپیلن، پلیاستایرن، اتیلن وینیل استات، واكسها با وزن مولکولی پایین، پلیمرهای آلكیدی یا پلیمرهای مخصوص دیگر تشکیل شده است. این پلیمر پایه اساس اصلی مستربچ است و ویژگیهای مکانیکی و شیمیایی محصول را تعیین میکند.
- 2. افزودنی:
مواد شیمیایی افزودنی به مستربچها اضافه میشوند تا خواص پلیمرها تغییر یابد. این افزودنیها شامل افزودنیهای بهبوددهنده خواص، پیگمنتها و پرکنندهها میشوند. نوع و میزان افزودنی بستگی به نوع پلیمر پایه و خواص مورد نظر دارد.
- 3. عامل سازگارکننده:
عامل سازگارکننده بهعنوان یک عامل مهم در پخش افزودنی یا رنگ به مستربچ ایفای نقش میکند. این عوامل معمولاً با پلیمر مذاب سازگار با ماده نهایی مصرفی ترکیب میشوند. استفاده از موادی مانند پلیپروپیلن گرافتشده با مالئیک انیدرید (PP-g-MA)، پلیاتیلن گرافتشده با مالئیک انیدرید (PE-g-MA) و ABS گرافتشده با مالئیک انیدرید (ABS-g-MA) باعث بهبود سازگاری شیمیایی افزودنیها با پلاستیک پایه میشود.
در فرآیند تولید مستربچ، استفاده از تجهیزات مناسب نیز بسیار حائز اهمیت است. بهطور کلی، از دستگاههایی با توانایی ایجاد نیروی برش مناسب، مخلوطکن و کنترلگر دما برای ایجاد یک مخلوط یکنواخت استفاده میشود. این فرآیند بهوسیله تجهیزات مناسب، تأثیر مستقیمی بر کیفیت نهایی مستربچها دارد. افزایش دما در اثر اختلاط، باعث افزایش چسبندگی پلیمر مصرفی میشود که این امر به بهبود خواص محصول کمک میکند.
انواع مستربچ
در دسته بندی مستربچها میتوان گفت، مستربچهای اصلی عبارتند از مستربچ افزودنی، رنگی و پرکننده.
مستربچهای افزودنی برای ایجاد خواص فیزیکی و شیمیایی خاص در محصول نهایی به کار میروند. در این دسته، مستربچهای نانو پایه PE، PP و UPVC بهمنظور بهبود خواص مکانیکی و ضربهپذیری مورد استفاده قرار میگیرند. شرکتهایی مانند رنگین پلیمر پیشگام در تولید مستربچهای افزودنی با تنوع ویژه هستند.
- مستربچهای نانو افزودنی
این نوع مستربچها از نانو افزودنیها برای بهبود خواص مکانیکی و ضربهپذیری استفاده میکنند. معمولاً از پلیمرهای PE، PP و UPVC به عنوان پایه استفاده میشود.
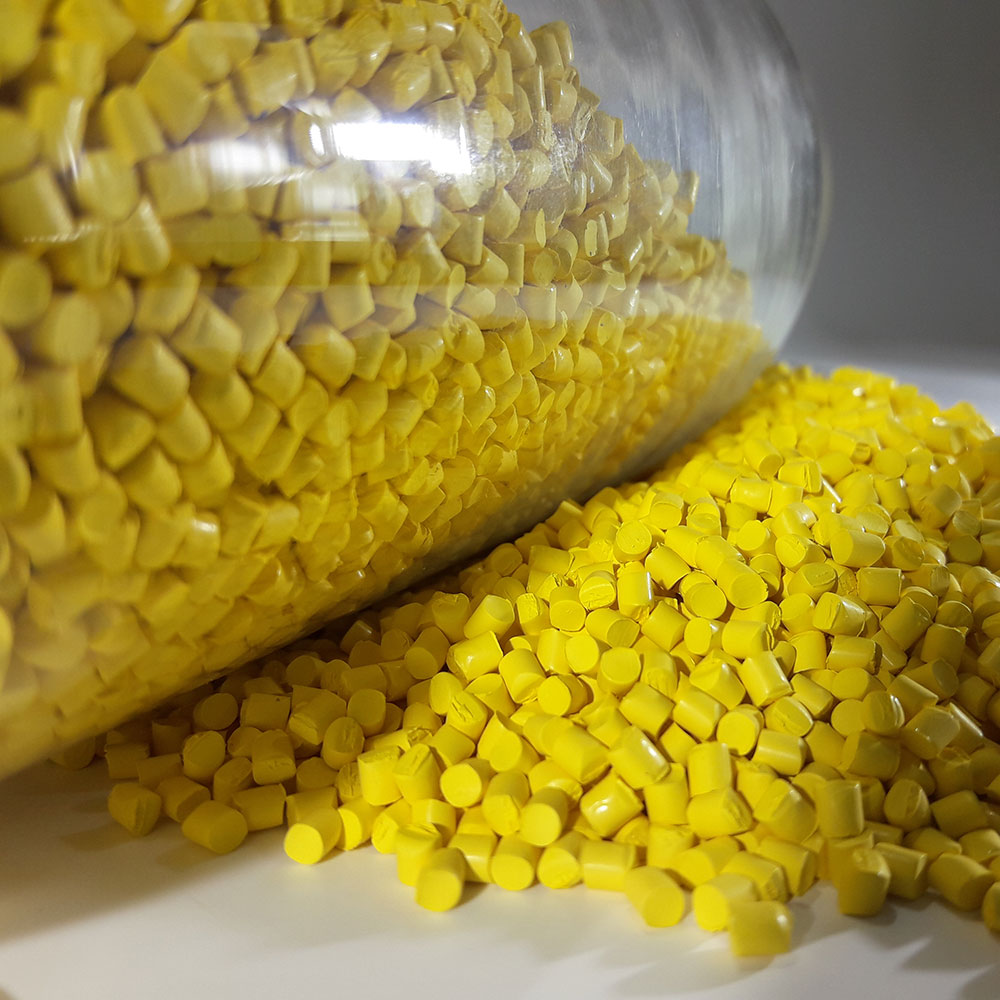
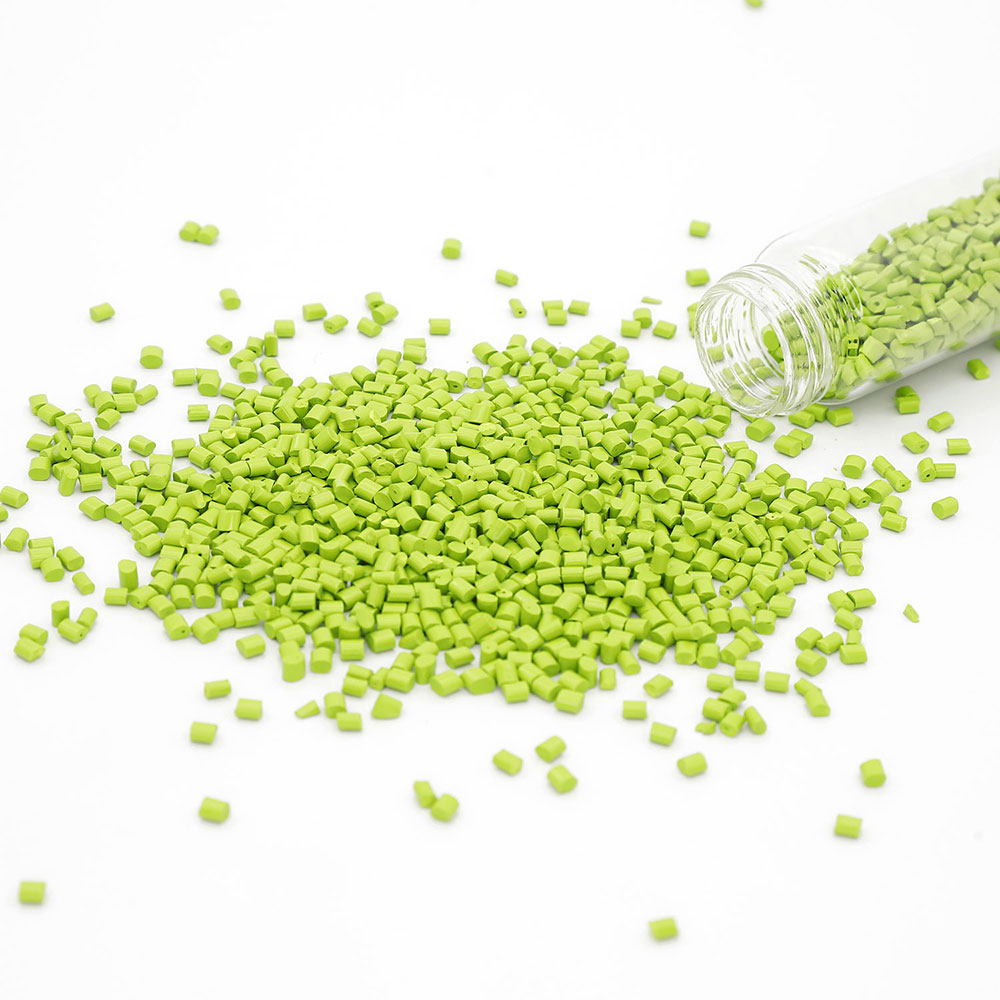
- مستربچ شفافکننده PP یا هستهزا
این نوع مستربچها به شفافیت پلیپروپیلن افزوده و آن را از طریق سازماندهی مولکولی در حین فرآیند بهبود میدهند. این مستربچها بهطور عمده در تولید محصولات شفاف و قطعاتی که نیاز به انتقال نور دارند، مورد استفاده قرار میگیرند.
- مستربچ لیزکننده PP و PE
پس از تولید فیلمهای پلاستیکی، لایههای فیلم با مشکلات جداشدن از یکدیگر در فرآیندهای بستهبندی روبرو میشوند. مستربچ لیزکننده این مشکلات را حل کرده و باعث لغزندگی بهتر و کاهش چسبیدگی سطح محصول (مخصوصاً فیلم و ورق) به قطعات فلزی میشود. مستربچ لیزکننده پلیاتیلن برای مصرف در نایلون، نایلکس، و فیلمهای چند لایه مناسب است، و لیزکننده پلیپروپیلن (مستربچ پ پ لیز) برای سلفون مناسب است.
در تولید فیلمهای پلیمری، مستربچ آنتی بلاک بهکار میرود تا چسبندگی سطوح فیلمها به یکدیگر پس از تولید و تا زمان مصرف را کاهش دهد.
-
- مستربچ روشنکننده نوری یا براقکننده PE
این مستربچ با نامهای مواد سفیدکننده پلیمر، مستربچ شفافکننده و عوامل سفیدکننده فلوئورسنت شناخته میشود. برای براق کردن و رفع کدری محصولات پلاستیکی بهکار میرود و با عبور نور بیشتر، جلای بیشتری به مصنوعات پلاستیکی میدهد. در فیلمهای معمولی و نازک، ضخیم، ظروف یکبار مصرف و مصنوعات پلاستیکی مختلف کاربرد دارد.
بهمنظور اصلاح فرآیند بلورینگی و کنترل سرد شدن قطعات پلاستیکی تزریقی با تأثیر در فرآیند کریستالیزاسیون پلیمر مذاب و حفظ پایداری ابعاد و شکل نهایی قطعه استفاده میشود.
از دیگر محصولاتی که به طور گسترده در صنایع پلاستیک قابل استفاده می باشد مستربچ های کمک فرآیند پلیمری بوده که به منظور افزایش قابلیت اکستروژن مورد استفاده قرار می گیرد. در واقع این ماده شکست مذاب را به خوبی حذف می کند و تجمع سرقالب را به طور قابل توجهی کاهش می دهد. همچنین این محصول با کاهش درصد ژل خروجی تولید را افزایش می دهد.
- مستربچ پایدارکننده نور UV
مصرف این مستربچها به عنوان یک کمککننده، از آسیبها و تغییرات رنگی که ممکن است در نتیجه تابش اشعه ماوراء بنفش به محصولات پلیمری وارد شود، جلوگیری میکند. این ترکیبات به عنوان یک سد محافظ علیه اثرات تخریبی و تغییرات رنگ پیش آمده از تابش اشعه ماوراء بنفش عمل میکنند. از این روش به منظور حفظ استحکام و زیبایی محصولات پلیمری در معرض نور مستقیم خورشید و دیگر منابع اشعه ماوراء بنفش استفاده میشود.
- مستربچ آنتی اکسیدانت
استفاده از مستربچهای آنتی اکسیدانت، به دلیل امکان تحت تأثیر قرار گرفتن پلیمرها از سوی عوامل اکسیداسیون، امری حیاتی در فرآیند تولید میباشد. این مستربچها با عمل به عنوان عوامل پایدارسازی، جلوی فرآیند اکسیداسیون را میگیرند و از تخریب و تغییر خواص پلیمرها به علت تماس با عوامل اکسایشی جلوگیری میکنند. از این روش در مستربچهای آنتی اکسیدانت بهمنظور افزایش مقاومت پلیمر در برابر عوامل مخرب اکسیداسیون و بهعنوان یک پوشش محافظ برای پلیمرها بهکار میروند.
- مستربچ کمک فرآیند پلیمر
بهمنظور افزایش قابلیت اکستروژن، مستربچهای کمک فرآیند پلیمری گسترده در صنایع پلاستیک بهکار میروند. این مستربچ شکست مذاب را حذف کرده، تجمع سرقالب را کاهش میدهد، پدیده پوسته ماهی را حذف کرده و با کاهش درصد ژل، خروجی تولید را افزایش میدهد.
- مستربچ رطوبتگیر
بهعنوان یک ماده خشککننده و جاذب رطوبت در مواد پلاستیکی، پلیمری و نایلونی با مواد بازیافتی یا فیلر در فرمولاسیون، بهبود کیفیت و بازده محصول، افزایش بهرهوری و کاهش مصرف انرژی و براقیت محصول نهایی، و همچنین جلوگیری از مشکلات مربوط به رطوبت مانند تخلخل و ایجاد حباب کمک میکند.
دیگر مستربچهای افزودنی عبارتند از ضد حریق، ضد سایش، ضد شبنم (Anti Fog)، خشککننده، افزاینده MFI، تمیزکننده، ضد چسبندگی (Chill-roll Release)، تجزیهپذیر نوری، ضد میکروبی، کنترل چسبندگی، حفرهزا، بهتأخیر اندازنده شعله، کاغذی (Paper like)، صدفی رنگ (Pearlescent)، بهبوددهنده مقاومت به ضربه و فسفورسانس.
- مستربچ رنگی
روش رایج برای تولید قطعات رنگی از مواد پلاستیکی، استفاده از مستربچهای رنگی است. این افزودنیها، علاوه بر ایجاد رنگ دلخواه در محصول نهایی، میتوانند خواص فیزیکی و مکانیکی آن را بهبود بخشند. مستربچ رنگی شامل مخلوطی از رنگدانه با درصد بالایی و پلیمر با درصد کمتری است.
تغییر غلظت و میزان این مواد میتواند به نمونههای مختلف رنگی منجر شود. انواع مستربچهای رنگی شامل مستربچهای سفید، مشکی و سایر رنگها هستند. این مستربچها دارای پایدارکننده، روانکننده داخلی و خارجی و پایه پلیمری میباشند. انتخاب صحیح مستربچ در ترکیب با پلاستیک بسیار حائز اهمیت است.
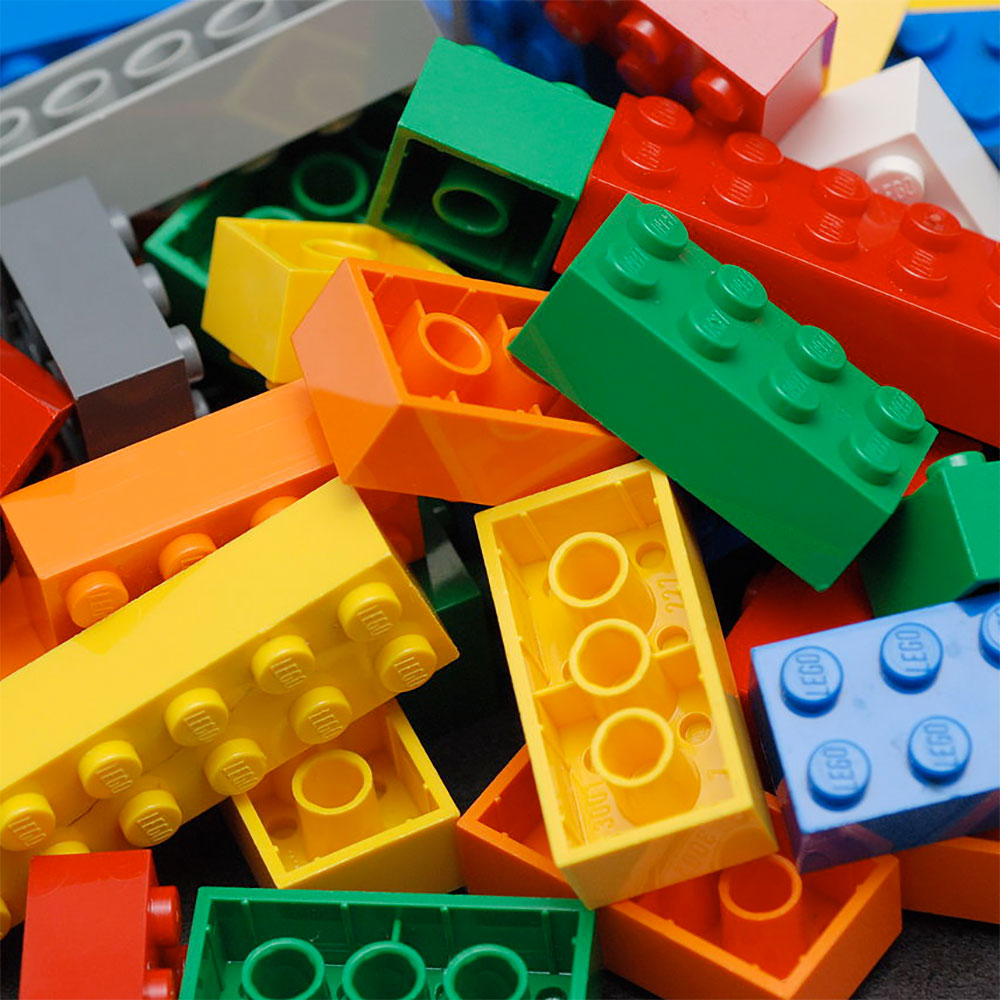
اجزای اصلی مستربچ رنگی
- رنگدانهها
شامل پیگمنتها در دو گروه آلی (مانند فتالوسیانین سبز) و معدنی (مانند اکسید آهن قرمز و یا تیتانیوم) میشود. همچنین رنگدانهها ممکن است به عنوان یک جوهر یا رنگ بیاثر شناخته شوند و عموماً برای رنگآمیزی پلیالفینها مناسب نیستند.
- سازگارکننده (پخشکننده)
وجود سازگارکننده در مستربچ رنگی دو اثر مهم دارد؛ از یک سو، باعث ایجاد ترشوندگی بر روی سطح رنگدانه میشود که نتیجهاش پخش بهتر پیگمنت در محصول نهایی است و از سوی دیگر، بدون تأثیر منفی بر کیفیت رنگ محصول، پلیمر را پایدار نگه میدارد.
- پلیمر حامل
این پلیمر باعث یکنواختی توزیع پیگمنت و سهولت در شکلدهی آن بهصورت گرانول میشود. سازگاری پلیمر با عامل پخش و همچنین تمایل بیشتر حامل نسبت به رنگدانه و پلیمر ضروری است. انتخاب پلیمر بر اساس شاخص مذابش بهصورتی است که بتواند مستربچ را بهخوبی حل کند.
با توجه به ماهیت شیمیایی پلاستیک، رنگآمیزی مناسب با رنگدانه را میتوان انتخاب نمود. برای مثال، رنگآمیزی پلیاتیلن، پلیپروپیلن و پیویسی را میتوان با استفاده از تیتانیوم به رنگ سفید یا با استفاده از اکسیدهای کروم به رنگ زرد یا قهوهای رساند. اما باید توجه داشت که از رنگهای ترکیبات آبی آهن نمیتوان در فرمولاسیون پلیاتیلن و پلیپروپیلن استفاده کرد.
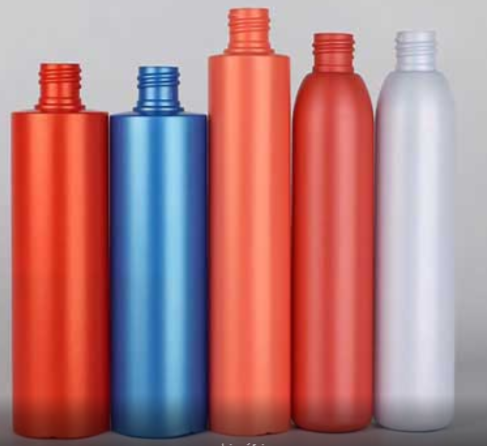
- مستربچ پرکننده
استفاده از مستربچ پرکننده به منظور کاهش هزینه و بهبود خواص مستربچ متداول است. این نوع مستربچها شامل مستربچ کربنات کلسیم، مستربچ تالک، میکا و سایر مستربچها میشوند.
مزایای استفاده از مستربچ
استفاده از مستربچها مزایای متعددی دارد که از جمله آنها میتوان به موارد زیر اشاره کرد:
- صرفهجویی در زمان و انرژی:
- استفاده از مستربچها به جای مخلوط کردن پودرها و نیاز به نیروی انسانی، زمان و انرژی را کاهش میدهد.
- این ترکیبات اقتصادی هستند و در فرآیندهای تولید به بهبود کارایی و صرفهجویی کمک میکنند.
- سهولت در ذخیرهسازی و جابهجایی:
- شکل گرانولی مستربچها باعث سهولت در ذخیرهسازی، جابهجایی، و کاربری آنها میشود.
- سادهتر شدن فرآیند تولید:
- استفاده از مستربچها منجر به سادهتر شدن خوراکدهی، تغییر غلظت افزودنی و یکنواختی رنگ یا خواص در حین تولید میشود.
- حفاظت از سلامت و ایمنی کارکنان:
- عدم پخش پیگمنتها در هوا باعث جلوگیری از خطرات سلامتی و آلودگی خطوط تولید میشود.
- کاهش مصرف افزودنی:
- بهدلیل یکنواختی بیشتر در توزیع مستربچ، مصرف مقدار کمتری از پیگمنت یا افزودنی مورد نیاز است.
- بهبود فرآیند ذوب:
- سازگاری عامل اتصالدهنده مستربچ با پلیمر منجر به بهبود فرآیند ذوب میشود.
- ثبات بیشتر خواص یا رنگ:
- استفاده از مستربچها باعث ثبات بیشتر در خواص یا رنگ محصولات میشود.
- کنترلپذیری بهتر در خصوص کدری و شفافیت محصولات رنگی:
- مستربچها به تنظیم کدری و شفافیت محصولات رنگی کمک میکنند.
- افزایش تکرارپذیری فرآیند:
- از طریق تعیین نسبت اجزای افزودنی مستربچ، تکرارپذیری در فرآیند تولید افزایش مییابد.
- حذف هزینه پاکسازی و تمیزکاری:
- استفاده از مستربچهای حاوی افزودنیهای تغلیظ شده، پاکسازی و تمیزکاری را کاهش میدهد.
ویژگیهای یک مستربچ خوب
فاکتورهای اساسی در انتخاب یک مستربچ با کیفیت مناسب عبارتند از:
-
- مستربچ باید بهطور کامل با پایه پلیمری مورد استفاده در تولید محصولات همخوانی داشته باشد تا تأثیر مثبت و یکنواخت بر روی ویژگیهای نهایی محصول داشته باشد.
- مستربچ باید در طول دفعات مصرف، ثبات رنگ و خواص را حفظ کند تا محصولات نهایی دارای کیفیت مناسب باشند.
- معیارهای فنی از جمله مقاومت انتقال سطح، درصد رطوبت، دمای ذوب، پراکندگی در ماتریس پلیمری، شکل ظاهری و جلای مستربچ، مقاومت حرارتی سطح باید با استانداردهای مشخص و مناسب برآورده شوند.
- مستربچ باید دارای غلظت یکنواخت و درصد مناسبی از افزودنی یا پیگمنت باشد تا اثر مطلوب در محصولات نهایی بهوجود آید.
- مصرف مستربچ باید کم و بهینه باشد تا به اقتصادیترین روش تولید برسد.
- مستربچ باید رنگ و شید منحصربهفردی داشته باشد که محصولات نهایی جذابیت بیشتری داشته باشند.
- مستربچ نباید در فرآیند تولید مشکلاتی ایجاد کند و باید به یکپارچگی و بهبود کارایی تولید کمک کند.
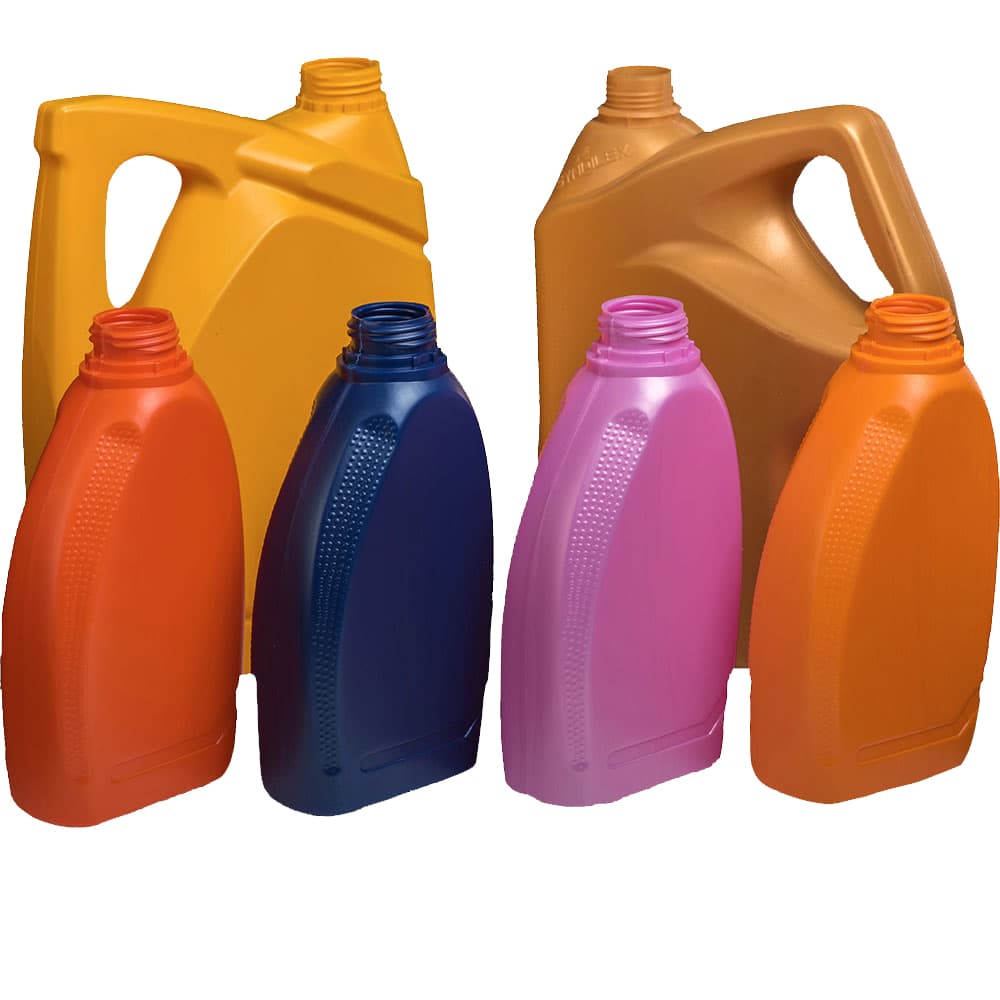
تولید مسترچ
۱- فرمولاسیون:
- این مرحله اولین و مهمترین مرحله تولید مستربچ است. در این مرحله، فرمول رنگ و میزان افزودنی به دقت مشخص میشود. مواد با سرعت بالا ترکیب میشوند تا نتایج بهتری حاصل شود.
۲- خوراکدهی:
- میزان تغذیه اجزاء با توجه به خروجی دستگاه تنظیم میشود.
۳- اختلاط:
- این مرحله شامل چهار مرحله است:
- خیسشوندگی پیگمنت، افزودنی و پرکننده.
- اختلاط فیزیکی: پیگمنت و افزودنی در پلیمر پایه پخش میشوند.
- توزیع: توزیع یکنواخت پیگمنت، افزودنی و پرکننده در مذاب پلیمری.
- پراکندهسازی: استحکام دهی به این مخلوط و جلوگیری از کلوخه شدن آن.
- مهمترین روش پخش، از طریق ترکیب اجزا بهصورت مذاب است. این مرحله با استفاده از دستگاههای مختلفی انجام میشود:
- مخلوطكنهای داخلی همانند بنبوری که مناسب برای تولید مقدار زیادی از افزودنیها است.
- مخلوطكنهای داخلی مداوم
- اكسترودر دو مارپیچ
- ماشینهای تك مارپیچ مانند Buss Ko-Kneader
- مخلوطكنهای سرعت بالا بههمراه اكسترودر تك مارپیچ
- مهمترین دستگاه استفاده شده در این فرآیند اکسترودر است.
۴- خط تولید:
- در این روش، پلیمر و افزودنیها در داخل اکسترودر ذوب و ترکیب میشوند. سپس از انتهای اکسترودر خارج میشوند. خط تولید شامل سیستم تخلیه، سیستم خوراکدهی، اکسترودر، سیستم خنککننده، سیستم برش، انبارش و بستهبندی است.
این مراحل با استفاده از تجهیزات مختلفی انجام میشوند تا مستربچ با کیفیت و خواص مناسب تولید شود.
سخن آخر
به صورت کلی مستربچ، شامل ترکیبات مختلفی از پلیمرها، پیگمنتها، و افزودنیها است. مستربچ نه تنها باعث بهبودهای ظاهری محصول میشود بلکه خواص مکانیکی و حرارتی را نیز تقویت میکند. با انتخاب و استفاده از مستربچ مناسب، میتوان به دستیابی به خواص دقیق و مشخصات تعیینشده در محصولات پلاستیکی را نیز فراهم نمود.
در واقع، استفاده از مستربچ به عنوان آخرین مرحله در فرآیند تولید، باعث بهبود کیفیت و قابلیت انطباق محصولات پلاستیکی با نیازهای بازار و مصرفکنندگان میگردد.
سوالات متداول
- مستربچ چیست و در چه صنایعی بهکار میرود؟
مستربچ یک ترکیب افزودنیها، پیگمنتها، و پلیمرها است که در صنایع پلاستیکی برای بهبود خصوصیات فیزیکی، مکانیکی، و ظاهری محصولات استفاده میشود. این ترکیبات معمولاً در فرم پلیمرها بهکار میروند و به محصولات پلاستیکی رنگ، لغزندگی، استحکام، و دیگر خصوصیات اضافه میکنند.
- چه مواردی در انتخاب مستربچ برای تولید محصولات پلاستیکی باید در نظر گرفته شود؟
در انتخاب مستربچ، مواردی مانند مطابقت پایه پلیمری با مواد تولیدی، ثبات رنگ یا خواص در دفعات مصرف، مشخصات فنی از جمله مقاومت انتقال سطح و دمای ذوب، و غلظت یکنواخت افزودنی یا پیگمنت بسیار حائز اهمیت هستند.
- مزایای استفاده از مستربچ در فرآیند تولید چیست؟
استفاده از مستربچ باعث صرفهجویی در وقت، انرژی، و هزینه میشود. این ترکیبات به سادگی قابل ذخیرهسازی و جابهجایی هستند، مصرف مقدار کمتر پیگمنت یا افزودنی را ممکن میسازند، همچنین خواص و رنگ محصولات را بهبود میبخشند.
- یک مستربچ خوب چه ویژگیهایی باید داشته باشد؟
ویژگیهای یک مستربچ خوب شامل مطابقت پایه پلیمری با مواد تولیدی، ثبات رنگ یا خواص در دفعات مصرف، مشخصات فنی مطلوب، غلظت یکنواخت و مناسب افزودنی یا پیگمنت، میزان مصرف کم، و منحصربفرد بودن رنگ میشوند.